预防圆锥破碎机“飞车”的措施介绍
- 字号 + -
在运行圆锥破碎机的时候,能允许长时间的剧烈“飞车”,一旦发现“飞车”故障必须立即停机检查。根据现场的具体情况,找出“飞车”的原因,采取相应的处理措施。以下粗略的谈谈预防“飞车”的常用措施和经验。
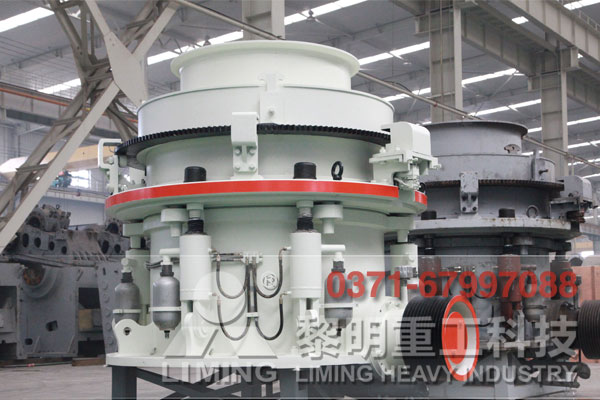
(1)主轴与锥套间合适的间隙对破碎机的运转至关重要。间隙太小容易发热“抱轴”而产生“飞车”,间隙太大又会产生较大的冲击和振动。SXHD-7′标准圆锥破碎机锥套上口与主轴间隙一般要大于2.74mm而小于3.2mm,主轴下端与锥套间隙为7-8mm左右。同时,对破碎机的另外两处间隙也要注意,偏心套与架体衬套间隙为3.2mm左右;大小伞齿轮啮合间隙,齿顶间隙为:3.175-7.925mm,齿侧间隙为:1.27-1.778mm。对于锥套与主轴之间的间隙通常检修时只检测上口间隙,用两段粗细合适的保险丝贴放在锥套上口(薄边、厚边各一段)。吊装锥体将主轴慢慢装入锥孔中,直至锥体球面压实在碗形瓦上,吊出锥体,检测两个挤压过的保险丝厚度,取其和即为实际锥套上口与主轴的问隙。对于锥套和主轴间的间隙调整可通过改变碗形轴承座与机架接触面的垫铁厚度来实现。测量大、小伞齿齿轮啮合间隙时必须注意:测量时,偏心套重边应在小齿轮侧,并使偏心套在小齿轮侧与大铜套全长接触靠近。
(2)对于锥套,在检修时一定要检查其薄边一侧与主轴的接触情况。若只有少数接触点(范围不足锥套高度四分之一,接触点在50mm×50mm面积内不足一点)。则要用角向磨光机或三棱刮刀刮研内孔高点,并用钢板尺边沿打磨处内孔母线方向检测,使尺边与母线之问均匀接触,目测没有问隙,粗磨达到要求。然后再把研磨剂涂抹在接触面,装入锥体空运转约10min后吊出检查,视接触点情况后再打磨。然后涂上研磨剂后再装入锥体空运转后视情况再打磨,如此反复直到锥套上口薄边一侧l/4~1/3高度范围内,与主轴保持均匀接触,每50mm×50mm范围内至少一点。若锥套上口出现一条沿母线方向的裂缝,其长度不超过200mm,且不影响锥
套与主轴的接触和间隙,仍可继续使用,但要在裂纹下端钻一个Φ8~Φ10mm的止裂孔。在实际工作中,锥套在偏心套的厚面不易磨损,若条件容许,可将锥套旋转180°研磨后再继续使用。若偏心轴套薄边—侧因受热向内凸起,要用磨光机打磨内孔,用钢板尺边沿锥孔母线方向检测,并将锥套插入与锥孔互研,视接触情况反复打磨、直至锥套能安装到位,与偏心套孔之间的间隙不超过0.1mm。
(3)动锥球面与碗形瓦的接触情况会影响锥体运转的稳定性,实践中发现触面多少在一定程度上可以控制动锥的自转。在动锥球面上均匀涂抹研磨剂,将动锥躯体与碗形瓦互研,使接触点均匀分布在碗形瓦半径的1/3~1/2外圆环内,并沿内圆周保持0.5~1mm楔形间隙,每25mm×25mm面积内至少有一个接触点,在其余半径l/2的内圆内不得有接触点。此外,碗形轴承磨损过大(油槽底被磨平),会使锥体下降较多,不能使动锥球面与碗形瓦内圆接触,这样会造成主轴与锥套间间隙过小,应更换新的碗形瓦。(4)针对偏心轴套上圆盘的磨损问题,可采取堆焊后车削修复圆盘的办法,如只有轻微磨损时,可在圆盘另一侧钻孔,调面后继续使用,为齿轮啮合间隙,装配修复的圆盘时,需要在下圆盘下面加合适的垫铁。
(5)圆锥破碎机各运动面上受有很大的的压力,且速度又比较高,所以正常的润滑对破碎机工作有着其重要的意义。在锥套与主轴之间要求润滑油既要有足够的粘度,保持油膜强度,又要有足够的流量和较低的供油温度,以带走摩擦热实现热平衡。为破碎机运转中得到充分的润滑,润滑系统与主电机、配套的给料机采用电气联锁。主电机开动前必须开油泵,否则主电机起动不起来;当油泵停止,压力降到0.05MPa或油温超过55℃时,均发出信号并停止给料机、主电机的运转,以机件不受破坏。由于油箱的容量有限,靠自然冷却是远远不够的,必须有率的换热器,回油温度控制在55℃左右,才能实现热量平衡。冬季可采用20"或30"机械油.夏季可采用50"机械油,一般温度可采用40"机械油。
上述是常见预防圆锥破碎机发生飞车的措施,其他这里就不一一详细的列举了,详情请咨询的我们的客服人员,或者留下联系方式,我们将有工作人员与您联络,或者拨打我们的工作热线:0371-67997088,将会有工作人给您做详细的解答。
如果您对我们的产品感兴趣或者有疑问,欢迎拨打我们的电话 0371-67997088 或者点击“商务通”在线咨询,我们的客服人员将为您提供详细的解答、周到的服务,您的满意将是我们前进的不懈动力,欢迎您的点击咨询。
欢迎转载《预防圆锥破碎机“飞车”的措施介绍》,转载请注明文章来源:https://www.lm-china.org/technology/826.html

- 全部评论(0)
下一篇:矿山机械液压故障分析